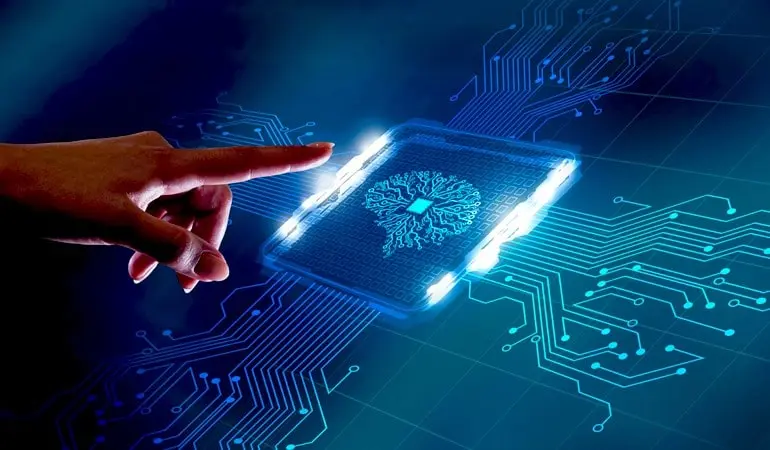
Have you ever come across the term Industry 4.0? Or the fourth industrial revolution, as others may call it? These terms reflect the defining characteristics of our age: rapid digitization and economic growth on the back of emerging technologies like artificial intelligence (AI), computer vision, machine learning, digital twins, the Internet of Things (IoT), cloud computing, and more.
Companies use these technologies to recreate products, streamline workflows, improve manufacturing processes, strengthen supply chains, and a lot more. These technologies are extremely powerful in their own right, but combining them takes things to an altogether different level.
In fact, modern digital solutions usually combine two or more emerging technologies to leverage their full potential. For example, cloud computing and artificial intelligence combine to create a new field called Cloud AI – it refers to organizations that provide AI services over the internet, e.g., Amazon, Google, IBM, etc.
This article talks about one of these emerging technologies and its crucial role in driving Industry 4.0 initiatives and achievements: digital twins. We will discuss the application and benefits of using digital twins.
But before we do that, it would be best to explain some basics first.
What is a Digital Twin?
Simply put, a digital twin (DT) is a virtual replica or representation of a real-world physical object, process, or system. It uses sensors to send real-time data for simulations. And although people confuse it with simulations, digital twins do not require engineers to input data manually, unlike simulations.
Instead, digital twins use the Internet of Things (IoT) sensors on a product, system, or process to generate their real-time simulations. These sensors enable you to monitor the performance of the physical entity – a product, process, or system.
Digital twins are also more flexible, reliable, and accurate compared to computer-aided design (CAD) solutions. They help you test your products and processes in different environments to see how they behave under various conditions. As a result, DT technology is rapidly transforming multiple industries, but none more so than the manufacturing sector.
It is changing industries on four levels. The four levels are as follows:
- Component level – it enables you to run digital performance tests of various machine components used for manufacturing various items.
- Asset level – allows you to test an asset in a digital environment.
- Process level – digital twins are often used to monitor the entire manufacturing process of a product, from design, prototyping, and development to finalize the logistics and shipping details. In fact, one can use digital twins to enhance the efficiency of any business process.
- System level – you can use DT to track how a system operates, e.g., an automotive assembly line.
How does it Work?
A digital requires certain things to work. It needs IoT sensors, the internet, and access to operational data generated by IoT devices. Today, manufacturers use machinery that already has sensors that collect real-time data. If a manufacturer uses older technology without in-built sensors, they will need to use IoT sensors to collect and transmit data.
IoT sensors collect data and send it to a cloud AI solution that processes it to create a digital replica of the same. However, the IoT data must first be processed and organized to enable the digital twin to work. Once you set it up correctly, the AI solution can simulate the real-world entity with complete accuracy, thus allowing you to conduct tests and run simulations in the virtual world.
All this occurs in real-time, as IoT sensors send real-time data to the AI solution for simulation. As a result, you can know exactly how your object (a process or product) functions at any given time.
Not only this, but the digital twin technology has a trump card, too – it lets you run future simulations for products, processes, and systems. Consequently, you can identify potential issues in advance and rectify them before releasing the product or implementing the process.
Digital Twin Applications in Industry 4.0
Digital twin adoption is rapidly growing across various industries. But its use is most pronounced in the manufacturing sector, leading to the emergence of smart manufacturing.
Smart manufacturing (SM) is a technology-driven approach that analyzes production methods and processes using machines and the Internet. Its goal is to improve manufacturing processes and enable automation wherever possible. It also uses IoT to achieve this.
Apart from the manufacturing industry, digital twins are used in the following sectors:
1. Energy
The energy sector also utilizes digital twin technology to improve power generation and consumption. It uses real-time data to monitor demand surges and identify which machine or equipment consumes more energy than others. This allows the company to optimize its energy consumption and bring down operating costs.
2. Automotive
The automotive industry lays great emphasis on prototyping and testing. The industry does this because, as we have seen quite often, a faulty car, once launched in the market, is recalled by the manufacturer due to problems with its machinery, etc.
This obviously costs car manufacturers a fortune. Billions of dollars are wasted. Digital twins help automotive manufacturers avoid such scenarios by identifying and rectifying errors in the product before it is released. Therefore, it reduces development time, removes operational bottlenecks, and reduces production costs.
3. Logistics
In a globalized world, supply chain management has become very challenging. Supply chains today traverse the high seas, spanning continents and oceans and the far corners of the earth.
In such an interrelated and well-connected world, managing a company’s logistics is an uphill task, even for the best of managers. It is tough to keep track of the flow of goods and people for a company with thousands of employees and hundreds of locations.
Digital twins help organizations overcome the complexities of modern supply chain management by allowing them to run simulations for different situations. A digital twin allows you to identify supply chain problems. It also provides you with solutions to fix the same, helping you enhance your decision-making process and improve the overall efficiency of your operations.
4. Healthcare
The healthcare industry is also utilizing digital twin technology for incredible purposes. It is facilitating surgery, training, organ donation, and much more. You can use it to improve patient outcomes as well as hospital management.
Moreover, digital twins give much-needed real-time monitoring capability to doctors and offer dynamic analyses followed by accurate treatment options. Similarly, you can use this technology to monitor patients when they are in their homes to track their recovery progress via IoT sensors and wearable devices. This capability enables doctors to make appropriate interventions at the right time, saving both money and time while improving patient health.
5. Disaster Management
Climate change is one of the leading concerns of humanity in the 21st century. Digital twins can help us create resilient communities by enabling us to build smart infrastructure, develop robust emergency response plans by simulating future scenarios, and monitor climate change.
The list of industries using digital twins is growing by the day, as are their use cases. We have only mentioned some of these examples.
Let’s look at some of the benefits and challenges of using digital twins in Industry 4.0.
Benefits of Using Digital Twins
- Real-time remote monitoring of assets, products, processes, and systems allows digital twins to help you improve efficiency and remove bottlenecks. It enables you to access the performance of your physical entities from anywhere in the world and control their performance and utilization.
- Digital twins improve risk assessment and quicken production times. You can test and validate your product’s performance before launching it. Not only this, but you can also try a product process before running it, thus saving yourself time and money by proactively addressing errors.
- Digital twins also let engineers test production systems by disrupting them and allowing them to gauge how they react to disruptions. Engineers can then develop mitigation strategies that come to the rescue in case of disruptions. All this helps improve risk assessment and reduce production costs and time.
- There’s a new game in the manufacturing industry: predictive maintenance. It refers to a set of techniques developed to identify a machine’s working condition and judge when the next maintenance should take place. This method, as opposed to preventive or time-based maintenance, helps you save costs by performing maintenance only when needed. Digital twins enable predictive maintenance by using sensors that predict when exactly a machine will require maintenance.
- The digital twin technology is also known for enabling and enhancing team collaboration through automation. Artificial intelligence- and machine learning-based systems learn how you manufacture products and then automate many of the repetitive tasks. This frees up your resources to focus on other matters. Automation also delivers more accurate data, thus improving decision-making.
Conclusion
Digital twins have made many things easy for companies, particularly manufacturers. A digital twin uses real-time data to help you cut costs, increase productivity, predict maintenance requirements, and improve overall efficiency. Companies use this technology to increase their return on investment, eliminate errors, enhance product quality, automate, etc.
Digital twins will continue to shape our industrial landscape in the coming years.
Do you want to learn more about how digital twins can help your company achieve its goals? Contact us at [email protected] to book a free consultation session with our team. Xavor is a leading technology firm based out of Irvine, California. We have served startups and Fortune 500 companies for nearly three decades.